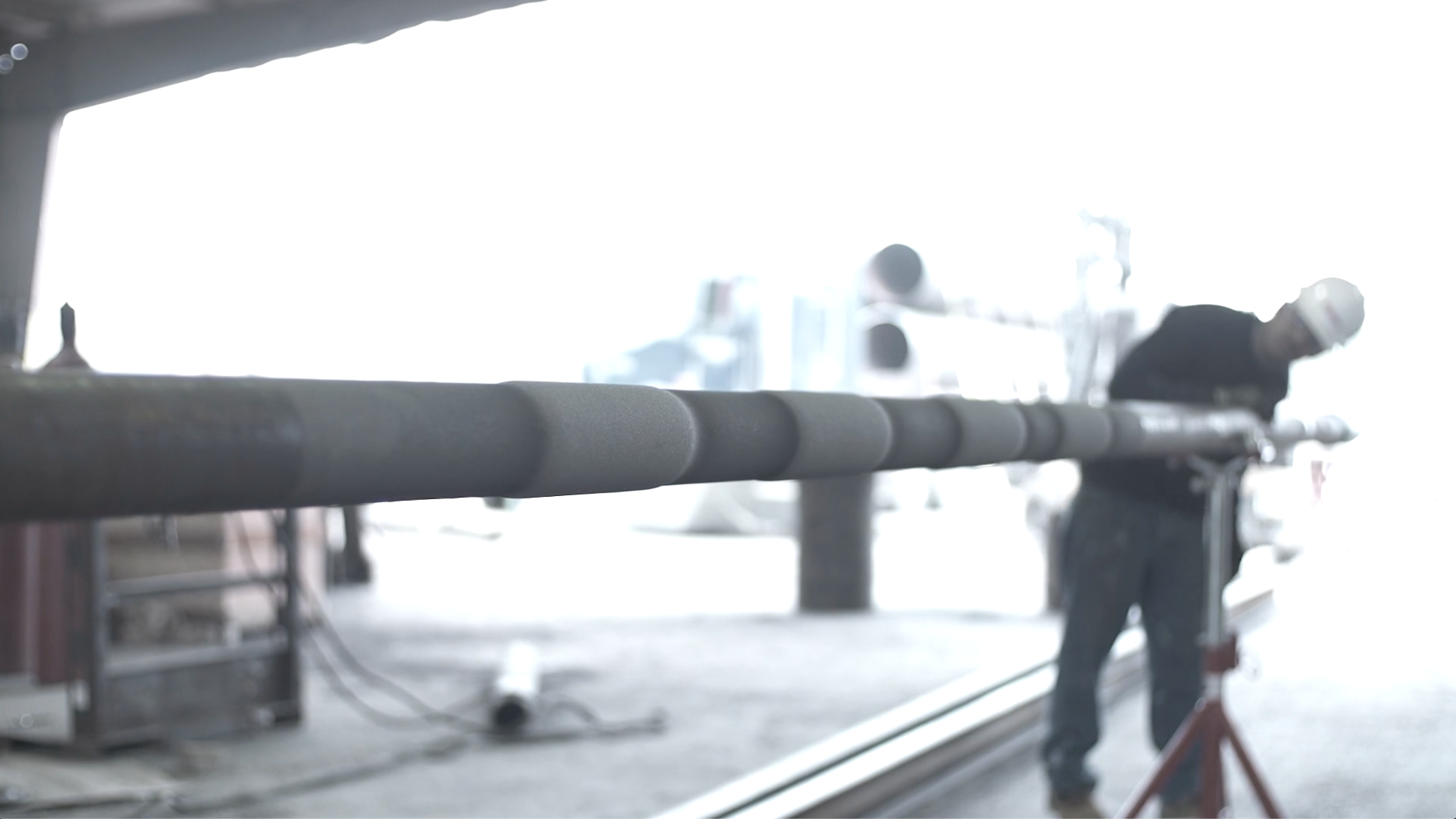
Drill Pipe Applications
Increase performance and reduce friction on drill pipe applications with RotoGlide.
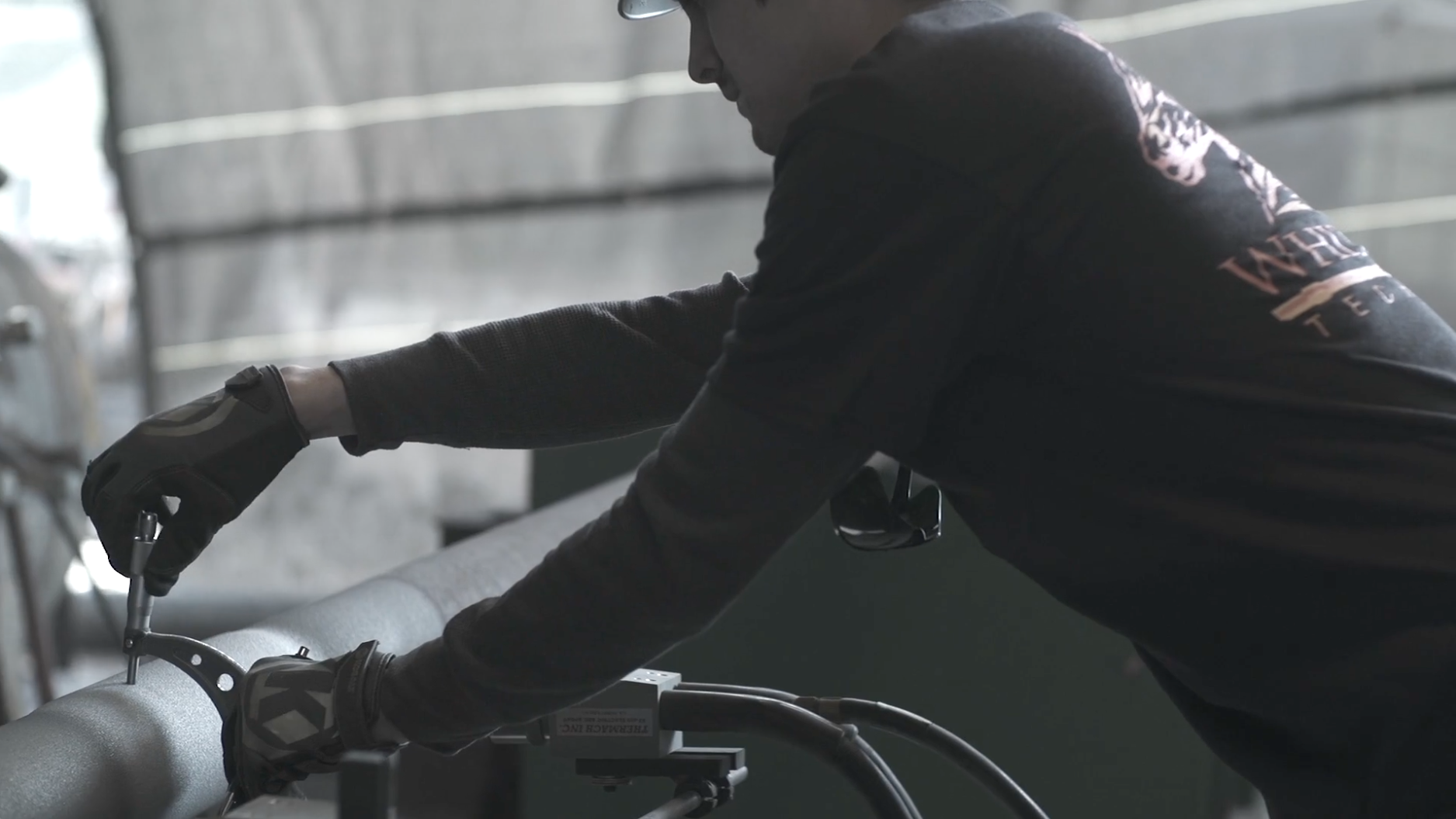
RotoGlide Features & Benefits
RotoGlide is unique in alloy design relying on boron carbides, (which are much harder than tungsten carbide) for wear resistance. These are dispersed in a very robust matrix that is essentially free of micro-cracks, which greatly improves spalling resistance and chloride induced crack propagation. Both the matrix and the boron carbide islands create a very low friction surface and a “casing friendly” contact area. RotoGlide has a very low friction coefficient (0.37) compared to steel (0.41) and tungsten carbide (.047).
Extends Drill Pipe Life
Eliminates DBR (Damage beyond repair) on Drill Pipe Joints. A Drill Pipe Joint with four bands of RotoGlide on the mid-body can drill up to 380,000ft of lateral section before it is worn out. Our customers reported that once RotoGlide becomes part of their Drilling String then DBR is non existing.
Reduced Torque & Drag
Field results show a reduction in torque and drag while drilling allowing to reach longer targets. Optimizing production and gained achievements per foot drilled in lateral sections. Performance results in decreased usage of lubrication subsequently reducing mud cost.
Proven Increase of ROP
RotoGlide has proven to allow for better string weight transfer, enabling more Weight on Bit (WOB) while drilling long lateral sections (10 – 14K) ft per well. Our customers have been able to double their ROP. A real time savings when your drilling operations are shaving off two days of drilling
Drill Pipe Protection
RotoGlide is a thermally sprayed alloy, designed to produce a robust, wear resistant and low friction coating for down hole tubulars, especially drill pipe. It is used successfully to greatly reduce mid-tube wear on drill pipe by providing a set of low friction “sleeve bearings” that produce stand-off from the open hole or casing.
The proof is in actual drilling experience in the severely abrasive shale formations in the Bakken.
Save the drill pipe tube from wear – the tool joints become the limiting useful life factor on DP life due to limited thread re-cuts.
Save typically 1-2 days drilling time due to low friction, greater weight on bit.
Lower mud lubricant by 50%,achieving the same torque and drag
Fewer inspections as the tube is not being worn nor damaged.
Used to restore yellow band pipe to service in the laterals.
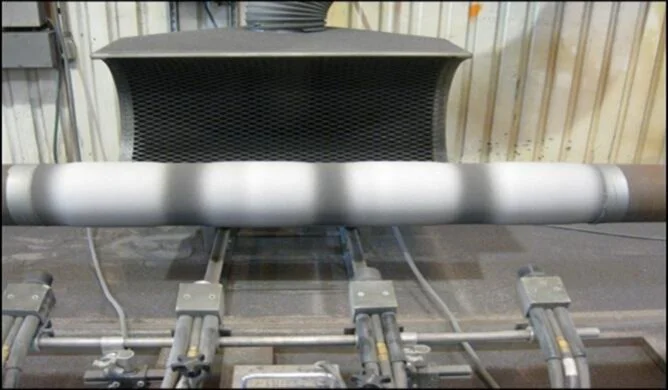
Wear Performance
Application
The above shows the application process and end result of a 6-5/8” drill pipe with four thermally applied mid tube wear bands. These bands help to significantly reduce torque and drag and decrease the volume of lubricating fluids needed downhole.
Drilling Performance Enhancement
Whitehorse Technology has a proven track record of drilling performance enhancement through enabling the operator to achieve more “weight on bit” by improving the placement of the drill pipe in hole. In addition to this significant torque and drag reduction has been achieved in lateral sections with the additional benefit of decreased volume of lubricating fluids. This enables operators to save millions of dollars in capital expenditures by making their core assets last longer. Our technology can be applied on new, premium and Class II drill pipe. Design and thickness of stand of dimensions is customized to customer request by application.